Multiplying Wafer Backgrinding Throughput:
Backgrinding Temporary Bonding Adhesive on Disposable Carrier
For backgrinding applications, traditionally, film-forming liquid waxes were preferred for their strong bonding to withstand vigorous shear force.
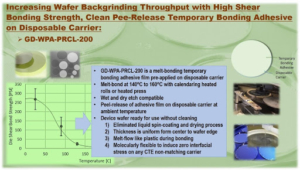
SiC and Sapphire wafer are much harder to back-grind and thin than Si wafer. High shear bond strength wax adhesive are the primary choice in backgrinding of these wafer.
In simplifying the processing in using wax-based adhesive, AIT pioneered the BGF wax films as the next generation solution for increasing the backgrinding throughput:
- µm level thickness and greater
- proven to save costs
- high uniformity
- For GD-BGF-7090 (also GD-BGF7160 for higher temperature) can be removed from the finished wafer with peeling at 90ºC or 160ºC respectively. The disposable carrier with the wax adhesive is disposed while the device wafer is clean with IPA at ambient easily.
GD-BGF 7090 and GD-BGF 7160: wax films on flexible disposal carriers (AIT patent-pending)
- Simplify processing and increase throughput
- No spin-coating
- No lengthy drying process
- No carrier to clean
- Same outstanding wax performance
- Remove from finished wafer with peeling at elevated temperature
- 90ºC for GD-BGF 7090; 160ºC for GD-BGF 7160
- Device wafer easily cleaned at ambient with IPA
GD-PRCL-200: novel, melt-bonding temporary bonding adhesive
- Outstanding shear bonding strength
- Peel-Release-Clean polymer technology: No residuals = No post-grind cleaning process
- Just peel it off, throw it out, and on to the next wafer
- For backgrinding applications without additional wafer processing:
- Temporary bonding adhesive should be as thin as possible
- AIT wax film adhesives can be as thin as 3µm
- PRCL (peel-release-clean adhesive): adhesive film thickness 10-20µm
They are designed for melt-lamination onto the wafer substrate using total thickness variation controlled calendaring or traditional pressure-vacuum lamination machines.

The above is a representation of the temporary bonding adhesive pre-applied onto the disposable carrier with the device wafer site in the middle. The temporary bonding adhesive area is extended beyond the wafer diameter for ease of removal post backgrinding. Also may be used for simultaneous mounting on tape-frame with wafer-substrate.
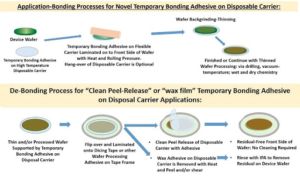
The processes in applying wax adhesive film onto device wafer to be thinned and de-bonding from finished wafer-substrate are great simplified for the increase in backgrinding wafer throughput per hour.
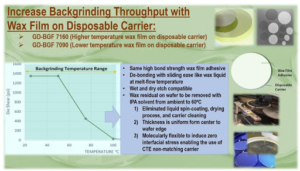
The patent-pending solution, AIT melt-conformable temporary bonding adhesive on disposable carrier is molecularly designed to have flexibility. It will not induce interfacial stress whether or not the disposable carrier and wafer have matched CTE. The elimination of spinning, drying and cleaning multiplies wafer throughput.