Wafer Processing Adhesive on Disposable Carrier for Multiplying Wafer Processing Throughput
Standard wafer processing uses the CTE (coefficient of thermal expansion) matched carrier such as blank wafer or glass as support structure holding down with vacuum chuck in performing the different processing steps including temperature as high as 250-350ºC. Matched CTE at around 7 ppm/ºC minimize the need to consider the interfacial stress due to the temporary bonding adhesives that are typically having vastly different CTE from 60 ppm/ºC and up.
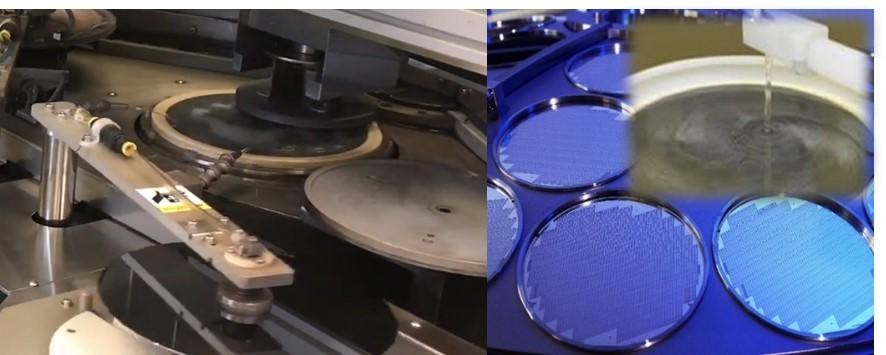
The key to the successes for the temporary bonding adhesive in wafer processing from backgrinding to 3D processing is to have high shear bond strength that are not affected by water during high shear backgrinding. The adhesive and holding strength during lithography, plating, processes under high vacuum, and a temperature for extended time from 200ºC to 350ºC.
AIT developed a temporary bonding adhesive that are extremely flexible and yet has strong shear bond strength during backgrinding and wafer processing. While these novel temporary bonding adhesives can be used with the traditional wafer processing using glass or wafer carrier described in separate section, with the use of disposal carrier, the wafer per hour throughput can be multiplied.
With the temporary bonding adhesive pre-applied onto the thin disposable carrier, the melt-lamination onto the active side of the device wafer is simplified. Besides traditional wafer temporary bonding equipment for vacuum assisted heated plate pressure lamination, AIT also developed a process for direct lamination using precision pre-heated calendaring roll lamination equipment for even faster throughput.
The biggest advantage with the use of the patent pending disposal carrier approach is in the de-bonding and separation of device wafer from the carrier. The following is an illustration of the difference in process of de-bonding:
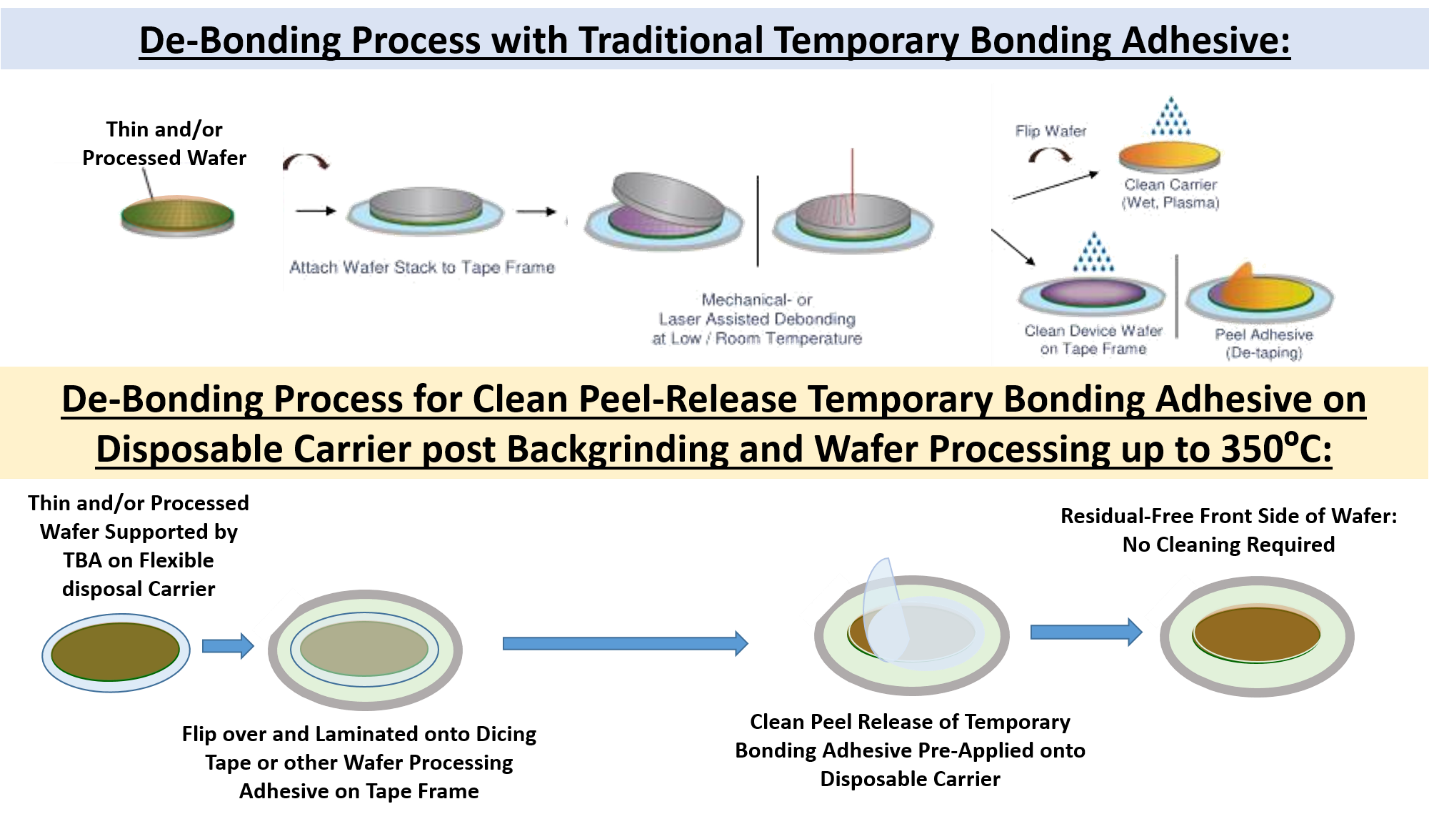
The above infographic of the de-bonding process with traditional temporary bonding adhesive and glass carrier to the AIT patent-pending clean peel-release disposable carrier. The GD-PRCL-350 temporary bonding adhesive is engineered to have strong shear bond strength will still peel-releasable clean from the device wafer while attaching to the disposable carrier. With the temporary bonding adhesive molecularly designed to have the ability to conform and stretch easily, the carrier may or may not have matched CTE to the device wafer and still will not impart interfacial stresses to cause finished wafer warpage.
The key of success is the molecularly engineered highly conforming and stretchable flexible temporary bonding adhesive having high shear bonding and high temperature stability.
- Pre-applied onto a disposable carrier removed several processing steps in deposition and forming tight total thickness variation of less than 5µm.
- The ability for the temporary bonding adhesive to peel-release from the device wafer without the use of heat-sliding and focused laser ablation that are relatively equipment and time intensive.
- In addition, the molecular structure having ability to peel-release clean without residual on device increases the number of wafer throughput per hour several fold.
- This disposable carrier with the adhesive layer is cost effective enough to be tossed.
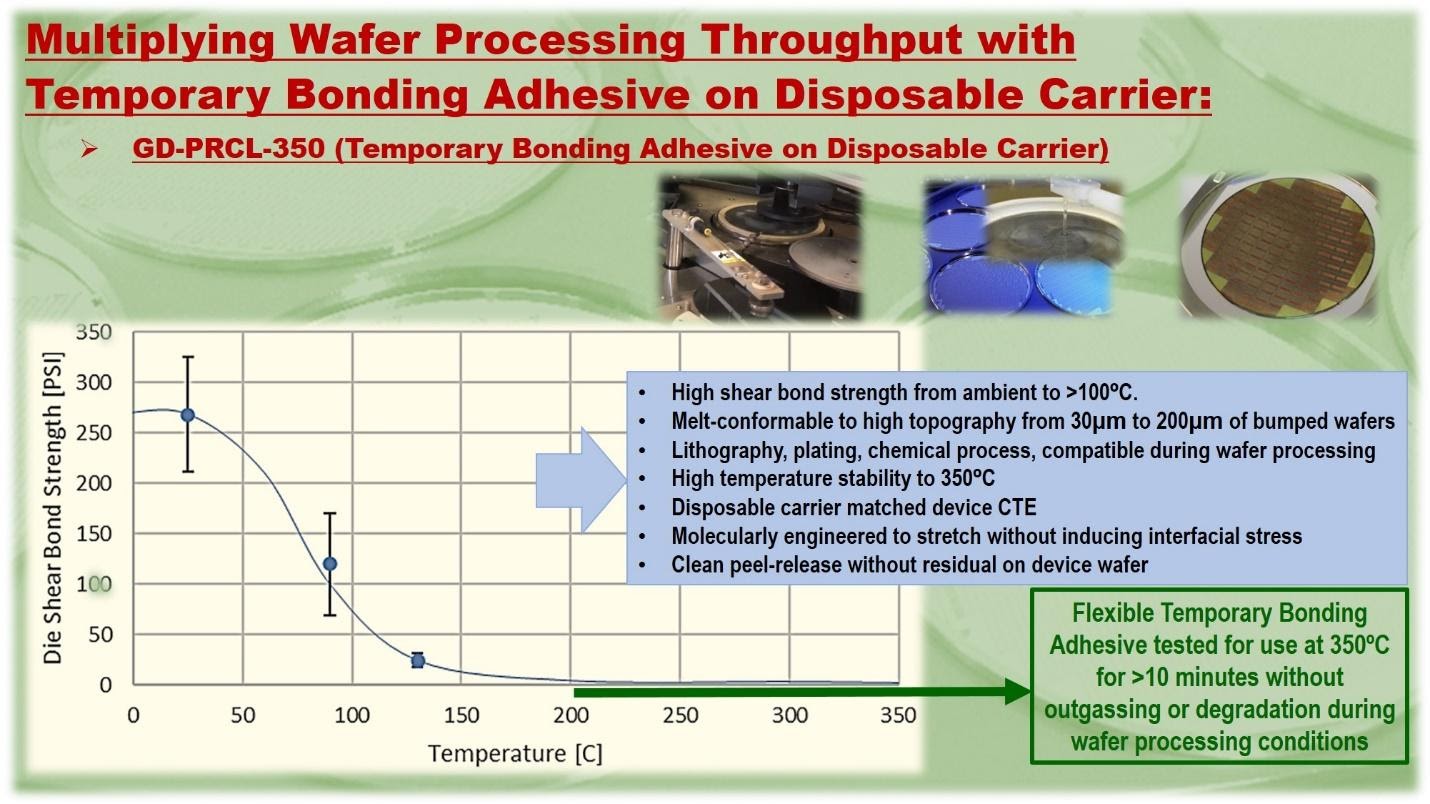
With this clean peel-release adhesive, after finishing backgrinding and wafer processing, the disposable carrier with adhesive can simply be peel-release clean from the device wafer. This extra simplification in wafer processing enables extra multiplication of wafer throughput per hour.
The following table details the properties of the three format of the AIT patent-pending temporary bonding adhesive on disposable carrier solutions.
- GD-PRCL-350-WS uses a disposable carrier that is closely matched to that of the device wafer such as silicon.
- GD-UVR-350-SS uses a disposable carrier that is not as closely matched to that of the device wafer.
- GD-UVR-350-FG uses a proprietary high temperature carrier that is translucent to transparent.